提高裂解炉热电偶投用率
发布时间:2020-02-26
浏览次数:
摘要:中国石油兰州石化分公司石油化工厂乙烯联合车间裂解装置SW
裂解炉热电偶是
表面热偶,由于运行时间较长、多次检修,致使表面热偶套管受热变形导致
热电偶插入不到位,与炉管接触不紧密,热偶保温密封不严等现象,造成温度指示失真,裂解炉横向温度分布不均匀,乙烯收率偏低。通过将热电偶套管由点焊改为满焊,使裂解炉热偶的投用率由60%~70%上升到90%以上,使裂解炉总是处于裂解深度下操作运行。
裂解是指石油系的烃类原料在高温条件下,发生碳链断裂或脱氢反应,生成烯烃及其他产物的过程。裂解目的是以生产乙烯、丙烯为主,同时还副产丁烯、丁二烯等烯烃和裂解汽油、柴油、燃料油等产品[1]。裂解反应有四个重要特点:①裂解反应是一个强烈吸热反应;②反应温度高;③停留时间要短;④烃分压要低[2]。
对于一个已定型的裂解炉,其出口温度反映了它的裂解深度,故裂解炉出口温度能影响裂解产物的分布和炉子结焦情况[1]。一般地乙烯、丙烯的收率随炉出口温度升高而增加,达到最大值后,温度再升高,则收率呈下降趋势。丁二烯的收率随炉出口温度变化不明显,甲烷、氢、重质燃料油的收率一般也随温度的升高而增大[3]。
1装置简介
石油化工厂乙烯联合车间裂解装置SW裂解炉是2003年兰州石化公司24万吨乙烯扩能改造新建的,由斯通-韦伯斯特公司设计6万吨乙烯/年SW-80U型裂解炉。至今已运行13年。该裂解炉的特点是双辐射室共用一个对流段,裂解炉均为“U”型管式,辐射炉管为双面辐射,主要特点是停留时间短、烃分压低、选择性高、乙烯收率高,运转周期长、热效率高,超高压蒸汽产量大,尤其裂解原料范围广,可以同时裂解多种原料,其中H炉可单独裂解石脑油、分区裂解石脑油和拔头油;采用底部烧嘴提供裂解所需要的热量。
2运行现状
(1)SW裂解炉辐射段有两个炉膛,每炉膛内有40根炉管进行裂解反应,每炉膛内有16只热偶,将16只热偶的平均温度作为每个炉膛裂解反应的温度控制指标,分别由TIC-1094/1095控制每个炉膛的裂解反应温度。
(2)SW裂解炉的热电偶是表面热偶,由于运行时间较长、多次检修,使表面热偶套管与炉管接触不严,套管受热变形导致热电偶插入不到位,保温密封不严等现象,造成温度指示失真,裂解炉横向温度分布不均匀,各组炉管出口温度差高达20~40℃,裂解炉热电偶能够投用的只有22左右,投用率只有68.75%。
(3)裂解炉由于热偶偏差引起炉温分布不均匀,裂解产物分布不合理,有时发生部分SLE发生泄漏、单根炉管结焦发红、甚至掉焦堵塞炉管等现象造成裂解炉频繁停炉检修,裂解炉运行周期不能达标;同时裂解产物分布不合理,乙烯收率在31.2%~34.67%之间波动,平均值只有33.22%。
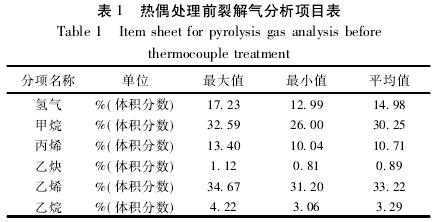
3热偶优化
(1)裂解炉热偶一般有两种测量方式,一是表面热偶,热偶测点在炉管的外表面;另一种是插入热偶,直接测量裂解气的温度。表面热偶具有外护套直接焊接在炉管表面,避开了裂解气高流速的冲刷,以及高温介质对测温元件的破坏,因此使用周期长;但是温度的滞后和受外界温差的影响都不能真正的反映炉管内的温度,给装置降低能、物耗带来了影响。而插入式热偶能反映真实的裂解温度,但受高温裂解气的磨损冲蚀,使用周期较短;为延长使用时间一般在运转一定时间后,将热偶套管旋转一定角度,避免裂解气朝一个方向冲蚀,保证热电偶套管在短时间内不被冲蚀漏,从而达到延长保护套管的寿命的目的。
(2)裂解炉出口温度反映了它的裂解深度,故裂解炉出口温度能影响裂解产物的分布和炉子结焦情况[4]。烃类高温热裂解生产乙烯时,裂解炉辐射段炉管内表面和急冷锅炉套管内表面伴随着焦炭的形成。这种高温条件下形成的焦炭是热的不良导体,会使炉管传热阻力增大、炉管内径变小,导致炉管外壁表面温度升高、炉管内流体压降增大,甚至堵塞管道,影响正常操作。当炉管外表温度达到炉管材质所能承受的高温度或者压降达到裂解炉的最大压降时,裂解炉必须进行清焦,清除管内的焦炭以后才能再次进行生产。
裂解深度、结焦母体的浓度及结焦反应的活性均随裂解温度升高而增加,裂解反应温度越高反应速率越快,二次反应越多结焦速率也越快。裂解温度瞬时的高温,会加深裂解深度,造成炉管的严重结焦。而且频繁的升降温,影响裂解炉管的使用寿命。
结焦速率和管壁温度有直接关系,结焦率决定炉子的运转周期[5]。随着清焦次数的增加,会对乙烯及副产品产量、燃料消耗、炉管寿命等带来不利影响,所以炉出口温度的控制精度是乙烯裂解深度和双烯收率的提高的关键因素。
(3)当裂解炉进料流量和压力、稀释蒸汽流量及压缩机人口压力确定后,停留时间随之确定,裂解温度即成为控制裂解深度重要的工艺参数,裂解炉操作首要是保持COT的平稳。稳定裂解温度的关键是稳定燃料压力,需要和分离岗位紧密配合,同时还要根据厂管网的加压火炬气进行综合平衡。
(4)SW裂解炉的表面热偶投用前安装位置一致,统一安装在炉顶板的保温层中,由于运行时间较长,裂解炉管受热发生蠕变,热偶套管位置发生位移,热偶测温点发生变化,使热偶温度指示产生横向偏差,从而影响了裂解产物的分布,对装置的能、物耗有较大影响。SW裂解炉的表面热偶套管改进前用点焊焊接在炉管外壁上,由于热偶套管与炉管使用材质的不一致,在炉子运行和停炉检修期间,两种材质膨胀系数不同,造成焊缝处裂开或不牢固。由于热偶投用时间较长,热偶套管受热变形,在临时抢修更换热电偶时,造成热电偶插入不到位,热偶温度指示产生偏差,从而影响了炉膛裂解温度TIC-1094/1095的指示。现在采用满焊10cm无死点,这样热偶套管与炉管的焊接面积增大,使得热偶套管与炉管表面接触更加牢固。
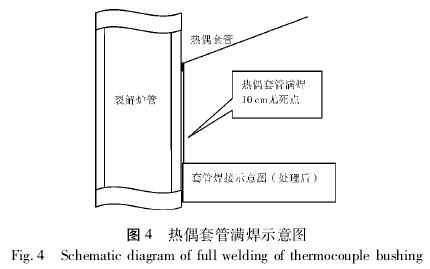
(5)通过将热电偶套管满焊,统一焊接的物理位置,统一更换新热电偶,裂解炉热偶的投用率由60%~70%上升到90%以上,各组炉管出口温度(32支热偶)差控制在5℃之内,横向温度分布更加均匀,使裂解炉总是处于裂解深度下操作运行。
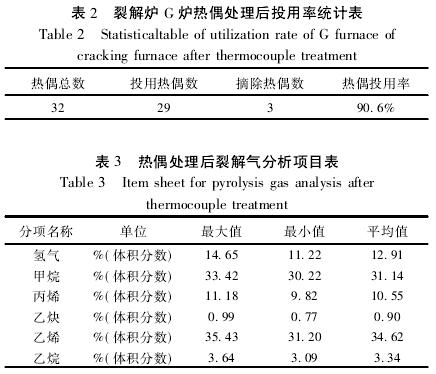
4结语
通过对热电偶的整治,热偶的投用率由60%~70%上升到90%以上,裂解温度得到有效控制,波动范围变窄,乙烯收率在33.7%~35.43%之间,平均值在34.62%,乙烯收率比处理前提高1.4%,按年产12万吨乙烯,每吨乙烯成本3500元计,单台裂解炉年增经济效益147万元,同时减缓了炉管的结焦,延长了裂解炉的运行周期。