分布式热电阻温度采集系统设计
发布时间:2020-09-03
浏览次数:
摘要:基于MAX31865数字转换器设计一套嵌人式温度采集系统,实现
热电阻温度传感器信号的采集。为减少引线电阻对测量结果的影响,采用三线制接线方式。
分布式热电阻信号经过数字转换器转换成数字信号,通过申行外设接口传送至单片机,实现温度的测量。该温度采集系统具备6路热电阻传感器信号采集、处理及显示功能。试验测试表明:开发的系统测量精度高,工作稳定可靠,满足使用要求。
0引言
温度是过程控制系统中重要的被控变量之一。
热电阻是工业中进行温度检测常用的元件之一,反应快,时间间隔相对较小,具有较高的精度、较好的长期稳定性,测温范围广,工作范围为-200~850℃可测特定部位或狭小场所的温度,对温度的调节、控制、放大等很容易进行。热电阻传感器(resistancetemperaturedetector,RTD)基于电阻随温度的变化而改变的特性进行温度测量。铂或铜等正温度系数热电阻具有较好的稳定性、线性输出特性以及较宽的测温范围,得到广泛应用。采集热电阻信号,结合遍历查表法、一次插值法和平滑滤波算法后得出温度;使用C8051F350芯片完成对热电阻信号的采集;采用ADC0832为A/D转换器,设计了一个检测范围为0~600℃的温度检测报警电路。MAX31865芯片是一款将热电阻模拟信号转换为数字信号的转换器,具有集成度高、分辨率高及可靠性高等优点,还具备故障自诊断功能,适用于对热电阻信号进行处理’。本文中基于MAX31865数字输出转换器及单片机设计一套热电阻传感器温度采集系统,以实现温度的精度高测量,并在发动机试验台架上对该系统的稳定性进行验证。
1系统整体结构设计
基于热电阻传感器以及MAX31865数字输出转换器设计一套温度信号采集、处理及通信检测系统,包括温度传感器、单片机、MAX31865数字输出转换器等,系统结构如图1所示。热电阻传感器的电阻随温度改变,传感器信号连接至MAX31865芯片。单片机依次控制各MAX31865芯片的使能端,实现温度信号至数字信号的转换,基于串行外设接口(serialperipheralinterface,SPI)总线,按照MAX31865传输协议得到各传感器的温度。采集系统通过RS-485通信将温度实时传给上位机,实现温度的显示。
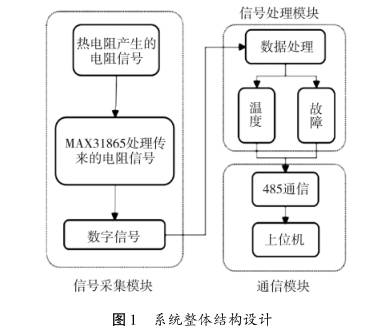
2系统硬件结构设计
2.1热电阻信号处理电路
系统的硬件部分包括热电阻处理电路、单片机及周围电路、电平转换电路和485通信电路等。本采集系统由6路电阻处理电路及其周围电路组成,可同时采集并处理6路电阻信号,使用MAX31865数字输出转换器处理热电阻模拟信号,该芯片内置15位模/数转换器,其精度可达0.5℃,并且具有±50V的过压保护输人,提供可配置的热电阻及电路开路、短路故障检测、SPI兼容接口以及相关的控制逻辑电路。每路热电阻信号处理电路如图2所示。图2中PT100为铂热电阻,即0℃时的电阻为100Ω。根据MAX31865芯片手册推荐,参考电阻应选择RTD0℃电阻的4倍。因此,PT100的参考电阻选用400Ω。热电阻采用三线制接线方式,为补偿导线上电阻的压降1-12],从差分输人(RTDIN+和RTDIN-)中减去FORCE+和RTDIN+的电压,利用FORCE2引脚对电阻输人进行采样。热电阻产生的模拟信号输人至处理电路,数字输出转换器采集并处理热电阻产生的模拟信号。
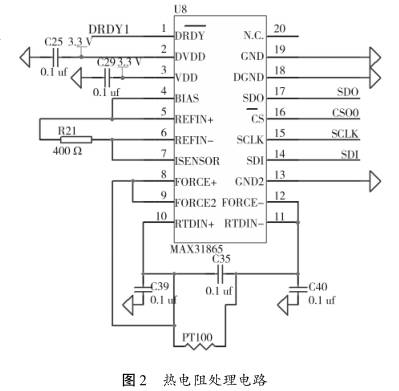
2.2单片机及周围电路
分布式热电阻温度采集系统采用MC9S08DZ60单片机进行信号处理。该单片机具有8位HCS08中央处理器,最高可配置20MHz总线时钟,支持最多32个中断/复位源,配置60KiBFlash存储器,最大2KiB的带电可擦可编程只读存储器(eletricallyerasableprogrammablereadonlymemory,EEPROM)在线可编程内存,最多可提供53个通用I/O管脚和1个专用输人管脚,管脚和片上外围设备(定时器、串行I/O、ADC、MSCAN等)共享,以及SPI模块提供微控制单元(microcontrollerunit,MCU)和外围器件间的全双工、同步和串行通信,满足装置的功能需求。
单片机及周围电路如图3所示,分为SPI通信电路、RS485通信电路和单片机周围电路等。单片机周围电路包括蜂鸣器及液晶显示器(liquidcrystaldisplay,LCD)灯电路,通过声音及LCD灯的亮灭状态可判断系统工作状态及故障情况。
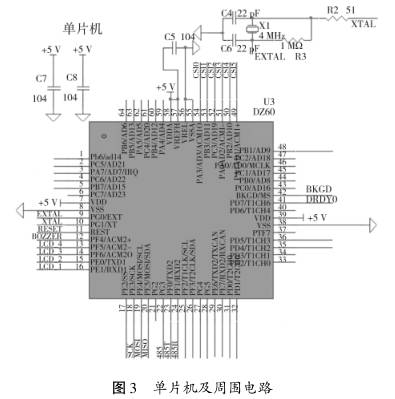
2.3电平转换电路:
由于热电阻处理电路采用的MAX31865芯片的工作电压为3.3V,故需将5V电源电压转换为3.3V.SN74LVC4245A具有三态输出的8路总线收发器和5.5V一3.3V双电源电平移位器。芯片分为A和B2组,一组输人,一组输出。其中A组支持1.5~5.5V电压,B组支持1.5~3.6V电压,A组供电电压大于B组。该芯片可实现5.5V一3.3V的电平转换,能够通过程序控制引脚实现转换方向的反转,电平转换电路如图4所示。74LVC4245的电平移位在其内部进行,双电源能保证两边端口的输出摆幅都能达到满电源幅值13-141,并且有很好的噪声抑制性能
:
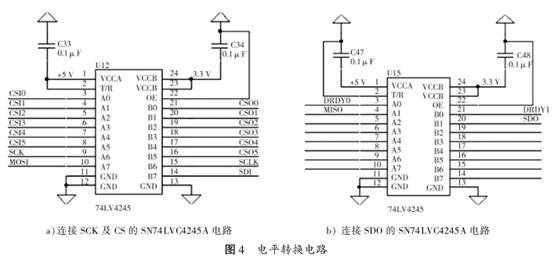
2.4RS一485通信模块
为了便于热电阻温度采集系统与上位机或其他系统关联,通过通信方式传递数据;考虑本系统对通信距离有一定要求,所以采用RS-485通信模块,实现热电阻温度采集模块与上位机或其他系统之间的数据传输,RS一485是由美国电子工业协会制定并发布的串行数据通信接口标准,具有传输距离长、速度高、电平兼容性好、使用灵活方便、可靠性高等优点[17-18],数据传输速率最高达到10MB/s,但仅在距离较小时可实现最大传输速率,当传输距离增大速率将随之减小191。RS-485通信电路如图5所示,图5a)为双通道数字隔离器及周围电路,用于隔离收发信号;图5b)为驱动器收发器集成芯片及周围电路;图5c)为光电耦合器及周围电路,用于隔离对RS-485通信电路的控制信号。通信电路接口采用的是差分接收器和平衡驱动器组合的方式,抗共模干扰能力较强。
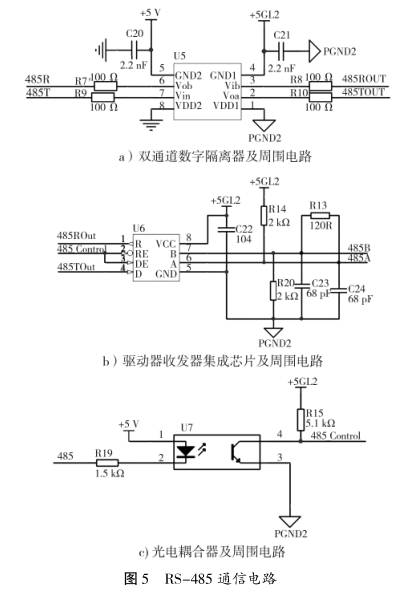
3系统软件设计
3.1RTD至数字输出转换器工作过程
热电阻在测量温度时接线方式有二线制、三线制和四线制2”,本系统中热电阻采用三线制接线方式。在程序中配置MAX31865各寄存器的值,在进行温度转换时系统可通过向配置寄存器D7位写1使能VBIAS。配置寄存器D6位为1时选择自动(连续)转换模式时,VBIAS保持有效状态;系统向该位写人0,退出自动转换模式,进入“常闭”模式,该模式下可发送单次转换命令。由于使用三线RTD连接,配置寄存器D4位为1。向D5、D3和D2位为0的同时向故障状态清零(D1)位写人1,将使故障寄存器的全部故障状态位(D[7:2])清零。
热电阻输人采集模块采用MAX31865芯片内部的15位ADC进行模数转换,转换得到的数字信号存放在两个8位寄存器中,高8位地址为0x01,低8位地址为0x02,其中低8位寄存器的最低位DO位为错误标志位。热电阻信号采集流程图如图6所示,转换模块在操作状态下采集模拟信号,通过使能片选信号(chipselect,CS)来选择某个通道,随后通过程序由单片机向MAX31865芯片发送读寄存器的指令,转换芯片收到指令后开始读取热电阻寄存器中存储的数值,若读取到低8位寄存器的D0故障位置位时,该通道故障,则将故障寄存器置位后将故障寄存器数值发送至单片机;若无故障,则将处理后的数字信号通过SPI发送传至单片机,由单片机进行计算得到当前热电阻所测温度,该通道热电阻信号采集结束。计算得到的温度可通过RS一485通信模块上传至上位机,由上位机做进一步的数据分析。
铂热电阻的电阻与温度的关系可用CallendarVanDusen方程表示[21为:
R(t)=R0(1+αt+bt²+c(t-100)t³),(1)
式中:t为温度;R(t)为温度t时热电阻的电阻;R0为t=0℃时热电阻的电阻;a、b、c为系数,其中α=3.90830×10
-3,b=-5.77500×10
-7,当-200℃≤t≤0℃,时c=-4.18301×100
-12;当0℃≤l≤850℃时,c=0。
在RTD的电阻已知且电阻特性定义良好的情况下,可通过式(1)确定温度。
MAX31865芯片可实现热电阻或电路连接故障的检测,若在采集及处理信号过程中出现故障,则系统会停止工作并将故障信息一并发送至单片机,故障检测流程图如图7所示。
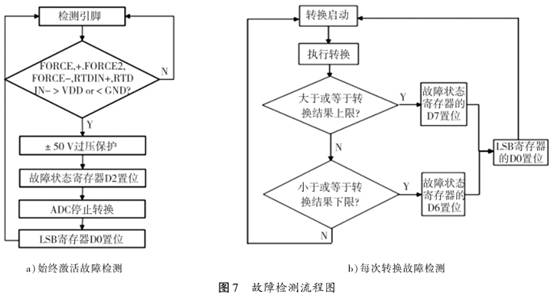
芯片在任意时间始终激活对FORCE+、FORCE2、RTDIN+、RTDIN-或FORCE-引脚的电压检测,具有高达+50V的输入电压保护。由图6a)可知,在任意时间点检测到发生过压(大于VDD)或欠压(小于GND1),开关开路,故障状态寄存器的D2置位,模数转换(analogtodigitalconverter,ADC)中止数据转换更新,直到故障解除后恢复转换。芯片在每次进行ADC转换时对检测结果进行检测,由图6b)可知,ADC启动转换后执行对模拟信号的转换,在检测到转换数据大于或等于转换结果上限时将故障状态寄存器的D7置位,小于或等于转换结果下限时将故障状态寄存器的D6置位,所有故障信息在LSB寄存器
D0置位后将信息传输给单片机。
3.2单片机软件设计
系统通电后,单片机首先完成系统初始化,包括时钟初始化、定时器初始化、I/O口初始化等;系统按照程序设定完成初始化后,进入正常工作模式。单片机依次使能各通道的CS信号,通过SPI通信从MAX31865数字输出转换器得到温度数据,并通过RS-485通信方式将各路温度数据发送至上位机,实现上位机的温度显示及存储等操作。
4试验测试
4.1温度标定
在恒温油槽中对该分布式热电阻温度采集系统进行标定,在20~120℃,每隔20℃对该温度采集系统进行标定。此次标定中,采用的恒温油槽适用温度范围为(室温+10℃)~300℃,温度波动范围为+0.05℃。使用所设计的分布式热电阻温度采集系统,在各标定温度下,使用各通道进行测量,得到各标定点温度下6个通道的温度如表1所示。由表1可知,各标定点工况下,该系统各测试通道的最大温度偏差均在0.5℃以内,系统各通道一致性较好。
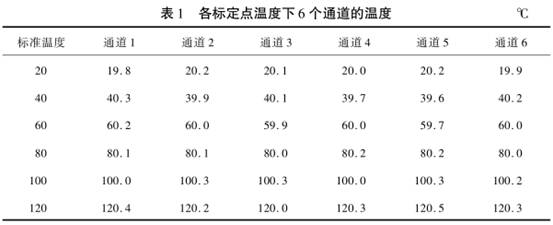
4.2试验测试
采用该测试系统对某公司生产的140柴油机进行性能测试试验,发动机转速为2100r/min,扭矩不同时,分布式温度采集系统同时采集主油道机油温度、增压器回油温度、油冷前机油温度和油冷后机油温度,如表2所示。
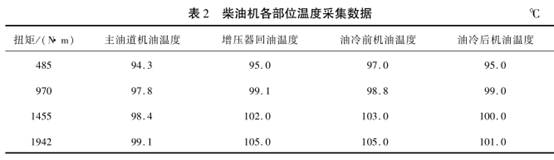
柴油机各部位温度随扭矩的变化曲线如图8所示。在研究所用工况下,由图8可知,随着扭矩的增加,增压器回油温度上升幅度最大,当扭矩由500N.m增至2000N.m时,温度,上升约10℃;上升幅度最小的是主油道机油温度。
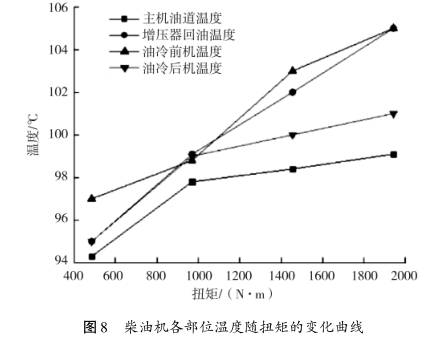
整个测试过程中,系统可以长时间稳定运行,可以实现精度高的温度测量,满足工业领域的温度采集要求。
5结论
1)基于单片机和MAX31865数字转换器设计了一套热电阻温度信号采集系统,系统具备六路热电阻信号采集、处理及通信等功能。
2)单片机依次控制各MAX31865芯片的使能端,实现温度信号至数字信号的转换,基于SPI总线按照MAX31865传输协议得到各传感器的温度。
3)采用该系统在发动机台架上,测量柴油机各处机油温度,结果表明,本系统工作稳定可靠,满足台架测试的要求。