基于热电偶测温的漏钢预报系统
发布时间:2021-05-17
浏览次数:
0引言
漏钢是连铸生产中的重大事故会损坏设备和扰乱生产计划甚至会造成人身伤亡,因此漏钢预报非常重要。为了保证连铸生产的稳定避免漏钢事故的发生,就必须在有可能发生漏钢的时候将其预报出来提醒操作人员进行相关处理。而在众多的漏钢事故类型中粘结性漏钢的出现概率为80%以上。粘结性漏钢是由于某种原因造成弯月面附近钢水与铜板的直接接触而发生粘结随着结晶器的振动及坯壳的下移粘结的钢坯表面在粘结部的下方被拉断破断处随着钢液的流入被修复但在下一次振动中又被重新拉断这样随着凝固的进行,断口不断下移,直到断口到达结晶器下口时钢水从断口漏出"。本文所指的漏钢预报主要是针对粘结性漏钢的预报。目前国内外预报粘结性漏钢的方法(2-31基本都基于
热电偶测温实现,即通过在结晶器壁.上安装热电偶阵列实时检测铜板温度然后通过I/0模块将热电偶的mV信号转换为数字信号再利用计算机程序对多组热电偶检测的温度趋势加以判断如果发现粘结特征就给予预警。
结晶器智能管理系统中的漏钢预报系统就是利用热电偶测温方法实现漏钢预报的。系统每秒收集一次结晶器铜板上的热电偶温度经过数据预处理后利用漏钢预报算法进行漏钢预报。
1系统结构.
漏钢预报系统主要由热电偶测温系统、端子箱、远程I/0站、PLC、交换机、测试终端和系统终端组成硬件结构如图1所示。
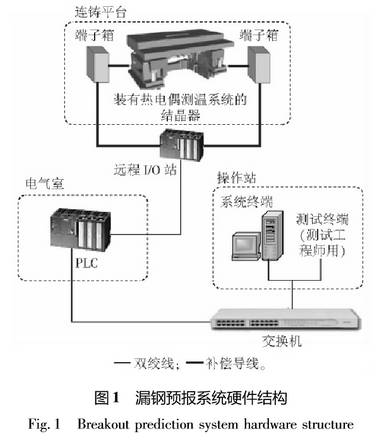
图1中热电偶测温系统由
K型铠装热电偶和耐
高温补偿导线组成。热电偶测得的mV信号经补偿导线进入端子箱进而进入远程I/0站然后通过I/0模块将数据传入电气室PLC,测试终端、系统终端的所有数据均通过交换机从电气室PLC.上获得。
2热电偶埋设方式
基于热电偶测温的漏钢预报系统中热电偶的个数和布置位置对漏钢预报算法的参数估算以及预报正确性起决定作用。
2.1热电偶个数
燕钢2号板坯连铸机热电偶的安装方式为垂直于结晶器壁插入K型耐高温铠装热电偶宽面3行11列窄面2行2列。结晶器内宽面的粘结点-般都在弯月面附近所以在宽面弯月面附近布置3行共计33个热电偶即可全面覆盖结晶器宽面铜板温度场;而结晶器窄面温度流场波动较大且反应灵敏,因此在窄面弯月面以下布置2行共计4个热电偶即可测出窄面的粘结特征。这种热电偶安装方式大大提高了漏钢预报的精度。
2.2热电偶布置位置
确定热电偶个数后,要根据漏钢预报子系统采用的算法布置热电偶(4]。由于漏钢预报子系统是通过对纵向和横向的热电偶组温度进行模式识别判断是否发生粘结性漏钢事故的,所以下面以宽面第1行发生粘结为例说明如何计算热电偶布置时的行间距及列间距(窄面的布置原理与宽面相同)。粘结区域一般呈V型若宽面第1行发生粘结则当粘结区域扩散到宽面第2行时粘结区域扩展示意图如图2所示。
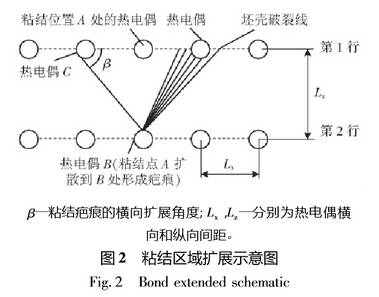
设热电偶A处为粘结点产生的位置该粘结点同时向下方和左右扩散。tz为粘结点从位置A纵向扩散到热电偶B处所需时间;tx为粘结点从位置A横向扩散到热电偶C处所需时间;V,为粘结点的纵向扩散速度;Vx为粘结点的横向扩散速度;V为拉速。热电偶布置的原则是期望纵向热电偶组(A与B)和横向热电偶组(A与C)同时判断出漏钢事故即tz=tx则有
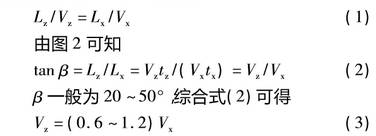
由式(3)可知粘结点的纵向扩散速度为横向扩散速度的0.6~1.2倍。因此,无论宽面还是窄面在布置结晶器热电偶时都可采用式(4)进行设计。

3漏钢预报算法
按照上述方法布置热电偶后,如果钢坯表面发生粘结以窄面为例,上行热电偶会先测得温度先升高后下降的趋势紧接着下行热电偶也会测得温度先升高后下降的趋势。通过分析热电偶测得的温度变化趋势,如果漏钢预报算法判断出即将发生漏钢漏钢预报系统会发出报警信号过程级向基础级发送降速指令基础级的拉矫驱动系统会自动降低拉速到设定值维持一段时间(根据现场要求而定)后即可恢复正常生产即通过漏钢预报系统避免了漏钢事故的发生。
漏钢预报系统采用逻辑判断方法和神经网络判断方法进行漏钢判断。由于系统投入初期数据样本数量不足神经网络训练不充分,因此会使得预报结果误差过大。为了保证漏钢预报的正确率普遍采用的方法是在系统投入初期以逻辑判断方法为主神经网络判断方法为辅;等粘结特征明显的样本数据积累到-定数量后就可以以神经网络判断方法为主了。目前本系统的神经网络判断方法仍处在积累数据和参数调整的过程中。图3所示为宽面漏钢预报算法流程图,由于宽面为3行热电偶,所以判断流程比窄面要复杂。对于窄面来说,“综合处理”后只要第12行有报警即可发出漏钢预报。
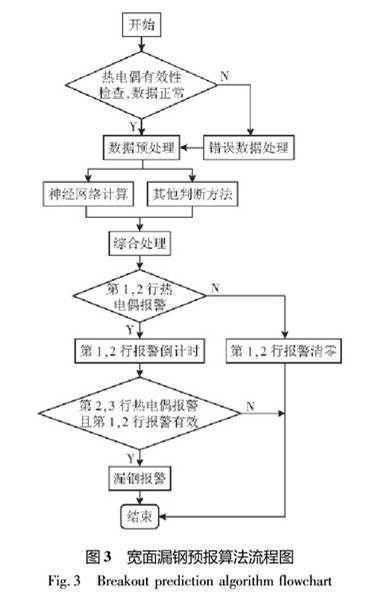
图3中的“错误数据处理”主要是针对故障热电偶所做的错误数据处理处理后可以用故障热.电偶修正后的温度参与到漏钢预报判断算法中,从而保证预报的正确性。首先需要对热电偶是否出现故障进行判断判断原则是:
(1)若热电偶测得的温度大于300C且超过30s则认为热电偶故障。
(2)若上行热电偶与下行热电偶测得温度的平均值之差连续100次小于某特定值(根据现场情况取值不同)则认为热电偶故障。
(3)若热电偶温度连续波动10次以上,且波动值都大于某特定值(根据现场情况取值不同),则认为热电偶故障。
然后,对故障热电偶测得的数据进行处理处理方法为:对当前故障热电偶相邻所有热电偶测得的温度取平均值后作为修正值参与漏钢预报计算。
图3中的“逻辑判断方法”是指同时满足以下
所有条件则判断为出现粘结性漏钢事故:
(1)热电偶与同列、同行相邻热电偶测得的温度差值大于某阈值ao
(2)热电偶在最近200s内测得的平均温升大于某阈值b。
(3)热电偶在最近30s内测得的平均温升大于某阈值c。
(4)相邻两个热电偶测得的温度变化率大于某阈值do
(5)最底行热电偶(宽面为第3行窄面为第2行)测得的温升大于某阈值e。
(6)对宽面来讲第3行热电偶测得的温度高于第2行热电偶测得温度的次数超过某阈值f;对窄面来讲第2行热电偶测得的温度高于第1行热电偶测得温度的次数超过某阈值g。
在结晶器热电偶的安装方式,如热电偶的行数、列数、间距和埋入深度等发生变化的情况下,逻辑判断方法中的各判断阈值也会发生变化。
综上所述燕钢2号板坯连铸机投入使用的漏钢预报子系统采用的逻辑判断方法为:根据对粘结性漏钢机理的分析和对现场数据的定量分析提取适当的逻辑条件来预报漏钢事故的发生。由于各种粘结性漏钢机理还不十分完善所以漏钢预报逻辑判断方法中的各阈值需根据经验在现场调试中确定。
4应用效果分析及改善措施
燕钢2号板坯连铸机漏钢预报系统自2011年5月上线以来,已经成功预报多次粘结性漏钢事故但是仍存在误报情况分析发现误报原因如下:
(1)热电偶接触不良或结晶器端子箱内进水等故障会导致热电偶测得的温度出现偏高或偏低的现象。
(2)热电偶信号在传输过程中发生失真导致逻辑判断方法得到的温度波动较大。
(3)结晶器液位波动导致热电偶温度检测结果波动。
通过总结误报原因发现大多数误报都源于热电偶的温度测量值不正确。因此,本文介绍热电偶维护及粘结性漏钢事故预防所采取的措施。
4.1热电偶维护
国内外漏钢预报系统普遍存在一一个问题:热电偶故障率较高。究其原因,或是热电偶的安装槽、热电偶补偿导线的现场端子箱存在油污及水蒸气或是用来固定热电偶的螺纹柱塞装置中的弹簧松弛或是热电偶的测温部分与结晶器壁没有接触到这些都会导致热电偶测得的温度数据不正确造成漏钢预报系统频繁出现漏报或误报。
为此热电偶安装时需要注意[6]:热电偶安装位置应尽量保持垂直使其测量端与铜板充分接触并且远离强磁场和强电场;热电偶应有足够的插入深度;采用带有弹簧的螺纹杆紧固热电偶使热电偶顶部与结晶器铜板完全接触;采用密封套对热电偶尾部的螺栓末端进行密封,防止油污及水蒸气进入;热电偶的现场端子箱是供热电偶和补偿导线连接用的其出线孔和盖子都需要用垫圈加以密封防止污物落入而影响接线的可靠性,且端子箱内要吹入高压空气以保证热电偶补偿导线航空插头的干燥;安装热电偶前通过加热热电偶的测温端检测热电偶及测温回路的质量,用万用表检查热电偶的电阻不合格的需要更换;判断补偿导线是否接地、短路及断路,如需要,加以修理或更换新的补偿导线;当热电偶插槽或现场端子箱内有污染物时,必须认真清洗热电偶端子箱内部并在干燥箱内烘干后再使用。
燕钢2号板坯连铸机使用的漏钢预报子系统,可以通过操作终端判断和确定热电偶故障原因并在操作终端的HMI.上给予提示。
现场应用时发现的热电偶故障原因及分析如下:
(1)若某热电偶测得的温度为1372C或者负数则说明无电势产生,应检查该热电偶丝焊接处是否断路热电偶补偿导线的现场端子箱内的端子是否接触不良。
(2)若某热电偶测得的温度比周围所有热电偶测得的温度低,应检查该热电偶是否没有安装到位(如热电偶的偶头与底部接触不到位)末端是否密封不好另外需要排除热电偶安装槽内是否进水。
(3)某热电偶测得的温度比周围所有热电偶测得的温度高,应检查热电偶安装槽内是否有油污或灰尘。
4.2粘结性漏钢事故预防
板坯连铸机粘结性漏钢事故的发生与现场操作工艺浇注温度、保护渣性能、结晶器振动以及结晶器内液面的波动等都有密切的关系。为了减少粘结性漏钢事故的发生,我们采取了以下措施'5]:规范换水口操作规范升降速制度(升降速的速率根据各钢厂情况而定)控制生产节奏避免频繁升降速确保保护渣性能;保持结晶器铜板与坯壳之间良好的润滑效果,做到少加渣、勤加渣在浇注过程中保证液渣能稳定流入结晶器壁和坯壳之间;定期检查设备尤其是对结晶器及热电偶的检查必须及时维护故障热电偶保证每行故障的热电偶不超过4个每行相邻的热电偶不能同时故障每列故障的热电偶不超过2个;提高结晶器振动以及结晶器液位控制技术的控制精度使结晶器内液位的波动范围在士5mm以内。这些措施--方面可以稳定生产从而减少粘结性漏钢事故的发生另--方面也有利于漏钢预报系统对粘结性漏钢事故做出正确判断进而防止粘结性漏钢事故发生。采取以上预防措施后,大大降低了粘结性漏钢事故的发生几率。
5结束语
目前国内大多数板坯连铸机都配有漏钢预报系统来预防漏钢事故的发生但是,仅靠它来预防漏钢事故是不够的规范生产、保证结晶器铜板与坯壳之间的润滑性才是预防漏钢事故的根本。