热电偶管断裂失效分析综述
发布时间:2020-06-04
浏览次数:
摘要:
热电偶套管断裂是它在实际应用中常见的失效形式,对该问题的研究方法进行归类说明,对断裂失效的一般原因加以归纳分析,对套管断裂的预防措施进行概括总结。
热电偶是测温仪表中常用的感温元件,在工.业生产、科学研究等领域应用广泛,它直接测量介质温度,并实时将温度信号转换为热电动势信号,再通过电气仪表转换为被测介质温度,以实现对温度的显示、传输和控制。由于多用于高温、高压、高腐蚀性介质及高流速流体冲击等场合,为保证温度传感器正常、安全、稳定工作,热电偶一般均设有套管保护川。虽然热电偶套管的设计初衷是为热电偶的正常工作提供保护,实际应用中也多能起到保护作用,但从目前热电偶发生故障的类型分析发现:套管断裂仍是常见的失效形式。对热电偶套管断裂的研究方法进行归类说明,对断裂失效的一般原因加以归纳分析,对套管断裂的预防措施进行概括总结。
1热电偶套管与容器壁连接
图1、2分别为一种热电偶套管结构及其与容器壁连接形式。
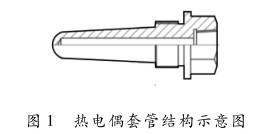
2失效分析方法
对发生断裂的热电偶套管进行分析研究,确立断裂原因,找到应对措施,--般会用到宏观断口分析、化学成分分析、力学性能分析、金相分析和扫描电镜分析方法。此外,腐蚀评价分析、模态分析和数值模拟分析在由结构腐蚀、强烈振动及流体冲击等造成的套管断裂分析中也是常用的方法。
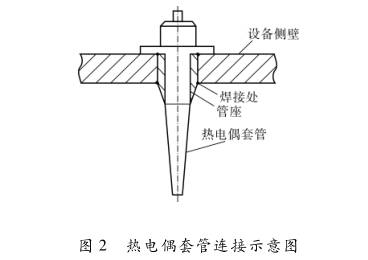
2.1 宏观断口分析
宏观断口分析一般用于在对热电偶套管断裂部位不作任何处理或经简单的超声波清洗后,确定断裂区位置及其附近构件整体状况、断面形貌特征、尺寸、瞬断区与扩展区区分、断口颜色分布、断裂部位平整度、光滑度、断裂类型、有无明显塑性变形、有无腐蚀斑点及有无咬边等焊接缺陷,以建立对套管断裂状况的初步认识,为进一步分析研究奠定基础[2]。图3为一热电偶套管断口宏观照片,断口表面平滑光整,并可见疲劳断裂特有的贝壳状花纹。.
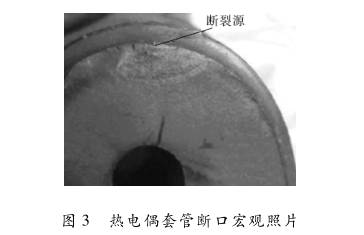
2.2 化学成分分析
在断裂的热电偶套管上取块状样品,利用化学分析或能谱分析方法,对套管基体材料的化学成分进行分析,主要确定实际材料各成分元素含量与牌号材料的有关规范要求是否相符,例如夏明六等对某断裂套管不锈钢进行化学成分分析[B]发现:其P元素的含量符合该优质钢材料的要求;但S元素含量偏高,而S含量的超标对该耐热钢的性能危害极大,可能引发该材料的热脆性[41) ,高温持久强度减弱,从而影响套管的使用寿命。
2.3力 学性能分析
热电偶套管的力学性能分析主要通过拉伸试验等确定材料实际力学性能是否符合标准力学性.能指标要求,文献[3]中对某材料为20Cr25Ni20的热电偶套管进行力学性能分析发现:套管的抗拉强度满足材料标准性能要求,而塑性低于20Cr25Ni20钢要求,拉伸试验后试样出现了-定的塑性变形。
2.4 金相分析
热电偶套管断裂的金相分析常取断口、焊接点和接头的金相样品,经碾磨抛光后,用适当比例的草酸溶液腐刻,再在显微镜下观察其金相组织,确定基体组织类型、焊接点熔合状况等。某热电偶套管金相显微照片如图4所示,经分析发现基体组织中碳化物颗粒数量较多,表明该套管材料的含碳量很高,进一步分析发现不仅碳化物数量多,而且其分布还呈明显带状,这将直接危害到钢材性能,导致材料产生各向异性[5。此外,硬度测试发现大量碳化物颗粒相的析出使得热电偶套管材料发生了明显硬化。
2.5 扫描电镜分析
扫描电镜分析一般是在金相分析基础上借助扫描电子显微镜对断口微观形貌作进--步的观察和分析,根据分析需要,通常要选择多个不同的放大倍数分别进行观察,是判断裂纹起源位置、扩展方向、扩展区大小、瞬断区形貌和断口特征,进而评价套管断裂原因的关键步骤。
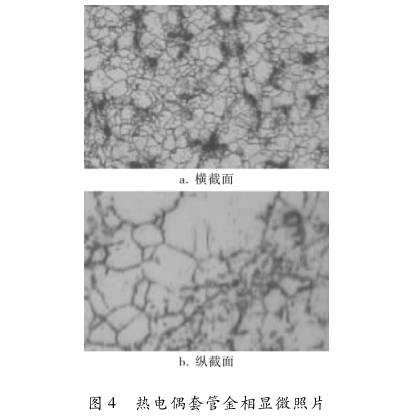
2.6 腐蚀评价分析
腐蚀评价分析并非必须选项,只是对一些存在明显腐蚀斑点,可能是由于腐蚀造成的套管断裂需要进行腐蚀评价。此外,对于一些断裂未处置时间过长,断口出现明显氧化物的热电偶套管也可能会进行有关腐蚀分析。.
2.7模态分析
热电偶套管断裂不少情况都是由于强烈振动甚至共振引起的,所以也时常会用到模态分析,模态分析既可能包括现场模态测试,也可能进行有限元模态分析方面的仿真研究,其目的通常都是为了确定结构和流体的各阶固有频率,尤其是对振动影响较大的低阶固有频率,应避免结构与流体固有频率相同或者相近。
2.8 数值模拟分析
在模态分析中提到的利用有限元分析软件(如ANSYS等)进行模态分析也属于数值模拟分析的范畴,但对于热电偶套管断裂以基于计算流体力学的方法(即CFD法)进行研究的情况也比较常见,如文献[6]采用大涡模拟方法对管流冲击热电偶套管进行了数值模拟研究,计算得到了热电偶套管的受力情况,并通过对结果的进一步分析,给出了减小热电偶套管受力的 有效措施 。
3断裂原因概述
热电偶套管断裂的原因多种多样,实际情况可能也各有不同,根据实地调研、实际经验结合相关资料,对常见的断裂原因作了总结:
a.焊接缺陷。对热电偶套管断裂位置进行统计发现,焊接处及其附近是断裂高发区域,这多.与焊接缺陷有关。文献[7]在对一减压转油线热电偶套管的断裂原因进行分析时提到由于焊接质量不良,热影响区组织不均匀,套管焊接的咬边缺陷使得外壁根部区域出现杂质偏析,微观组织也呈现出疏松、空洞等缺陷,在强烈冲击载荷作用下,产生裂纹并迅速扩展,最终导致热电偶套管断裂失效。
b.套管振动。连接热电偶套管的主管路通常充满流体,如果流体密度较大、流速过高,并呈现出湍流状态,便会在套管附近产生旋涡,当旋涡从套管两侧周期交替脱离时,在套管上会引起周期变化的升力和阻力,进而引起管内压力分布时刻变化,作用在套管上的流体压力和方向也不断变化,最后造成管路振动。当流体激振频率与套管固有频率相近甚至相同时,会发生共振。一旦产生强烈共振,套管内就会产生周期性的交变应力,长时间承受较大交变应力的套管,在一些应力较大部位就会出现疲劳断裂。
C.腐蚀脱落。热电偶套管常处于高温、高压及高湿度等极端环境和强腐蚀性等介质中,套管因为腐蚀而发生断裂失效的现象也时常发生,有些腐蚀可以通过肉眼直接观察,有些则需借助金相分析发现,例如晶间腐蚀,存在晶间腐蚀的地方也往往会成为疲劳断裂的裂纹源。
d.套管选材不当。热电偶套管对材料强度、耐极端环境等要求较高,常见的选材不当造成的套管断裂主要有3种情况,一是材料根本不符合相关标准要求;二是实际使用材料与设计选材不符(这是化学成分分析中常发现的问题,也是为什么要进行化学成分分析很重要的一个原因);三是选材侧重强度影响,缺乏耐高温高压、耐腐蚀等方面的考虑,或未考虑这些因素的长期影响。
e.热电偶安装位置不当。若热电偶套管断裂位置发生在弯头、孔板、大小头及阀门等元器件附近,那极有可能是由于热电偶安装位置不当造成的,因为这些地方都是产生激振力和能量较为集中的区域,所以如果不是温度测量和控制所必需的,热电偶的安装位置应尽量避开这些区域。
f. 热电偶安装方式不当。热电偶套管如果垂直安装在管路上,其受力状态可以简化为一悬壁梁模型,断口一.般发生在套管与主管路的连接处,该区域相当于悬壁梁的根部,是受力最大位置,也是容易产生应力集中的部位,所以对于倾斜安装也可以满足使用要求的热电偶可以选择以一定的角度倾斜安装,此外热电偶套管深人主管路的长度也是影响其断裂的重要因素,应合理选择。
4防范措施
通过对热电偶套管断裂有关原因和研究方法的分析,为避免类似故障的频繁发生,提出如下一些防范措施:
a.在满足材料选用一般原则和使用要求的情况下,提高热电偶保护套管的材料标准,如选用韧性较好、 抗腐蚀能力较强的材料等;
b.严格检查热电偶套管的内外质量、焊接质量等,避免因焊接不当,造成套管材料晶相组织改变,导致接头部位产生结晶裂纹;
C.在不影响温度测量需要和测量效果的前提下,合理选择热电偶的安装位置和安装方式,如改垂直安装为倾斜安装,可改变套管的受载情况;
d.选用新型防泄漏热电偶,这种热电偶在保护套管断裂的情况下仍然具备防止介质泄漏的功
能;
e.针对流致振动和共振引起的套管断裂,可以适当采用提高套管阻尼、加大壁厚及减小套管伸出长度等方法预防;
f.为了减少套管内流体旋涡脱落现象的发生,可以合理设计套管横截面形状和采用流线型表面,同时在成本范围内还可以在套管后安装旋涡干扰装置(图5)。
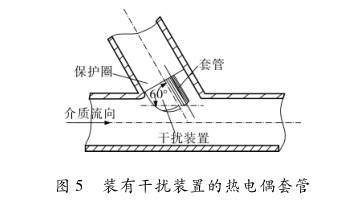
5结束语
热电偶套管断裂是热电偶应用过程中的常见失效形式,热电偶套管断裂的原因多种多样,如焊接缺陷、套管振动、腐蚀脱落、选材不当、安装位置或方式不当等是比较常见的原因。
为避免热电偶套管断裂事故的频繁发生,可采用科学选材、合理选择焊接工艺、合理选择热电偶的安装位置和安装方式、适当提高套管阻尼、合理确定壁厚和伸出长度、合理设计套管横截面形状和流线型表面、安装套管内旋涡干扰装置及选用新型防泄漏热电偶等方法。