有纸记录仪的特点与工作原理介绍
发布时间:2025-04-27
浏览次数:
有纸记录仪每个通道均可直接选择接收多种
热电偶、
热电阻、电压和电流信号,并可对被测信号进行数字显示及进行趋势记录和数字记录,能在本身打印的100mm宽的纸格上同时记录刻度值、时间及每一个信号的曲线,并将通道号印在各通道的轨迹旁。可通过键盘设定测量信号种类、小数点位置、显示范围、记录边界、报警值、回差、系统误差的校正、记录标尺、数据打印间隔、走纸速度、打印深度及时间等参数,并对所设参数加以保护。广泛应用于医药、石油、化工、冶金、电力等行业及科研单位。
有纸记录仪工作原理是每路输入信号经程控放大,24位分辨率AD转换,光电隔离送至单片机处理。从而彻底消除了各输入通道之间的干扰,消除了输入通道与CPU 之间的干扰。使用高精度数字温度传感器,进行热电偶的冷端温度补偿。为了提高长期稳定性,有纸记录仪放弃了传统的用电位器调整放大倍数及零点的方法,代之以软件程序调校法,并实现了放大倍数的程控放大。出厂前我们忠和测控均对各项参数均已调试完成。用户可通过键盘设定对系统误差进行平移校正。
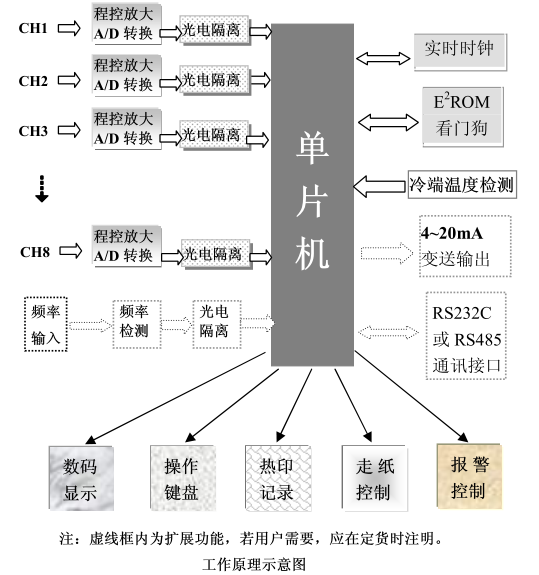