基于K型热电偶的输送带接头硫化感应加热系统的
发布时间:2021-02-24
浏览次数:
摘要:传统的输送带接头硫化加热方式存在加热不均匀、时间长、效率低等问题,为此提出了一种.基于电磁感应的输送带接头硫化加热系统。搭建了接头硫化感应加热系统的整体框架,然后通过COMSOL软件仿真得出通电线圈作用下的加热板温度分布云图,结合仿真结果,在钢板.上的不同位置布置
K型热电偶,通过
多路温度记录仪将测得的温度数据记录下来。结果表明:所设计的感应加热系统能够使硫化加热板均匀发热,且由K型热电偶与多路温度记录仪构成的温度监测系统能够对数据进行可靠的采集与处理。
0引言
输送带接头硫化机将接头两端无连接的钢丝绳在高温高压下用橡胶连接起来,形成一条完整的输送带甲。接头的强度主要取决于硫化阶段对胶料与钢丝绳物理成形的加热控制,而作为硫化机主要部件的加热板的表面温度均匀性会影响到接头的质量,对于输送带接头的硫化加热,目前存在多种方式:电加热、蒸汽加热.导热油加热等2.
蒸汽加热的缺点是在加热过程中,升温历程存在滞后性,可控性较差;电加热容易造成电能的浪费且升温较慢;导热油加热的缺陷在于整体结构设计较复杂。对于橡胶的硫化,有学者通过调整电磁的热参数解决了轮胎硫化的不均匀问题,但是对于电磁感应加热方式应用于输送带接头硫化的研究较少。
本文搭建了以电磁加热控制器调节线圈和电磁参数为基础的输送带接头硫化感应加热系统,通过COMS0L仿真得出感应加热下的热板温度分布规律,研究加热板发热的均匀性,并在实验平台中的加热板不同位置布置K型热电偶,以多路温度记录仪实时监测温度数据并显示出来,用以验证仿真结果的准确性。温度监测的结果表明电磁感应加热方式能够有效解决硫化加热不均匀的问题。
1输送带接头硫化感应加热系统的组成
电磁感应加热系统主要由线圈、加热钢板、电磁加热控制器以及温控仪组成,电磁加热控制器与温控.仪相连,温控仪的设定温度为150℃,此为硫化温度,其作用是使电磁加热控制器加热的温度稳定在±3℃范围内波动,使加热控制器以脉冲形式对钢板加热,达到均匀硫化的效果。
1.1电磁加热控制器
如图1所示,采用半桥单管5-8kW功率的电磁加热控制器,它可以将低频三相交流电以高频形式输出,具有IGBT过流保护功能D,同时有输出过流保护自动调节负反馈的功能(其中5kW功率下的电流保护点为22A,8kW功率下的电流保护点为30A),其内部采用高速输出电流霍尔传感器,能更精确地检测相位和电流大小4。采用高性能IGBT驱动芯片驱动,可以自动识别负载及锁相功能,以使负载端得到最高功率因数,也使电路精确控制在弱感区保持高效率工作。控制面板上有功能键,能够显示谐振状态、频率、电流、ICBT温度等。
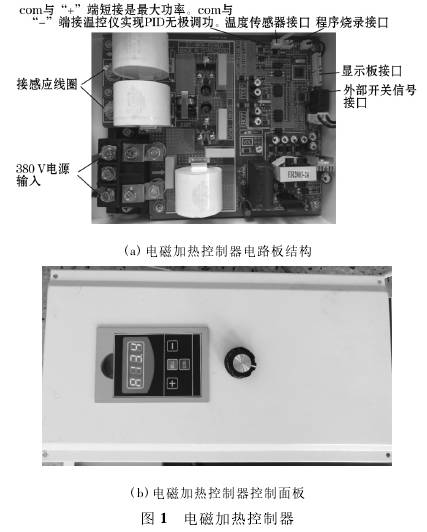
1.2线圈和加热钢板
电磁加热控制器可以通过控制流过线圈电流的大小和频率来控制加热钢板的升温速率,线圈通电后,由于交流电的影响,在其内外会产生与电流变化.相同的交变磁场,钢板置于这一范围内,钢板上就会产生与线圈相反的感应电流,感应电流在钢板上会形成封闭的回路,一-般被称为涡流,涡流的作用是使电能转换为热能,钢板才会发热国。接头硫化感应加热系统工作流程图如图2所示。
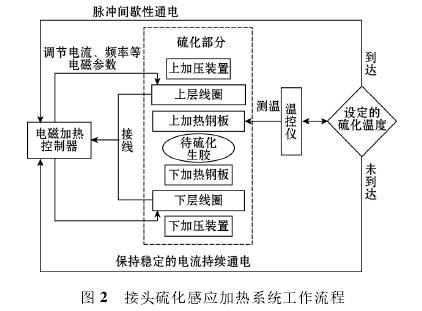
按照电磁加热控制器上的电路板的接线方式,依次将电磁加热控制器与电源线、温控仪和线圈相连,将温控仪调节到硫化所需的温度,接通总电源后调节电磁参数即可让系统正常工作,温控仪上设有传感器,将该传感器置于钢板上,用于探测钢板的温度是否达到所需的硫化温度,若未达到硫化温度,会控制加热器为线圈继续供电,直至测得钢板温度达到硫化温度,若已升温至目标值,温控仪将会使电磁加热控制器间断性地提供电流,以脉冲的形式进行加热,使温度保持在一稳定值。所设计的加热系统整体结构如图3所示。
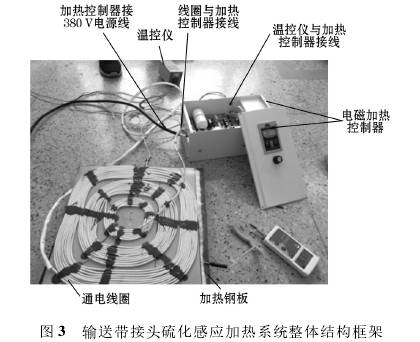
2加热仿真模型的建立与分析
电磁感应加热仿真模型主要简化为线圈和加热钢板,由电磁加热控制器的参数设定线圈的电感量,布置好线圈的排布方式,调节线圈与加热钢板之间的距离,建立线圈和钢板的三维模型(图4),表1为钢板的物理性能参数。
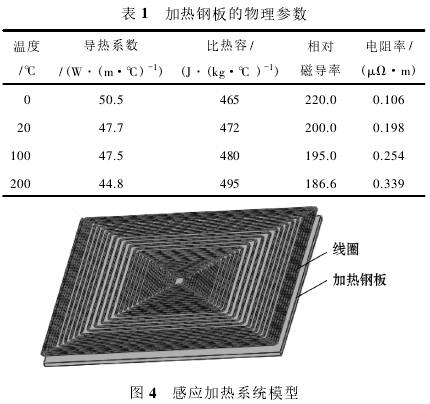
在COMSOL软件中研究线圈通电状态下热板的升温规律。钢板的尺寸设定为400mmx400mmX10mm。仿真的求解域是电磁场和温度场的耦合场,在软件中设置电磁参数,包括电流大小、频率、线圈匝数,在频域-瞬态的研究中将电磁损耗作为温度场求解的初始条件,最终可以得到感应电流的分布情况以及温度随时间的变化过程。仿真选取多种参数下的组合,设定线圈匝数为固定值,将电流大小和工作频率进行组合,设置的参数组合如表2所示。
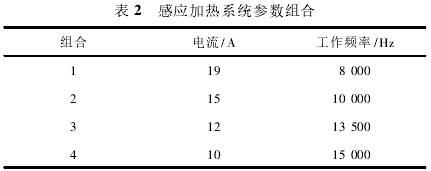
对表2不同组合下的线圈工作参数进行设置,可以得出4种条件下钢板的升温规律和温度分布云图,如图5所示。
可以看出,由于感应电流的作用,钢板表面的温度会逐渐升高,由于线圈中部位置的磁场强度近似为边缘端部的2倍,所以钢板4个边角处的稳定温度是最低的,由于涡流分布是由中心向边缘逐渐扩大,从而钢板中心位置处会出现加热死区,即中间部分某—区域的温度低于其周围温度。图5中4种工况下的温度分布趋势基本--致,电流越小,中间加热死区的面积也逐渐减小,与周围区域的温差也逐渐缩小。图中沿加热死区向钢板边缘端部过渡,会出现温度的极大值,原因是由于此处磁通密度较大,所产生的感应电流在此处汇聚密集,导致温度升高较快。由边角向中.心区域分析,温度是逐渐升高的,由仿真看出,随着电流的减小和频率的增大,钢板表面的整体温差是逐渐.缩小的。
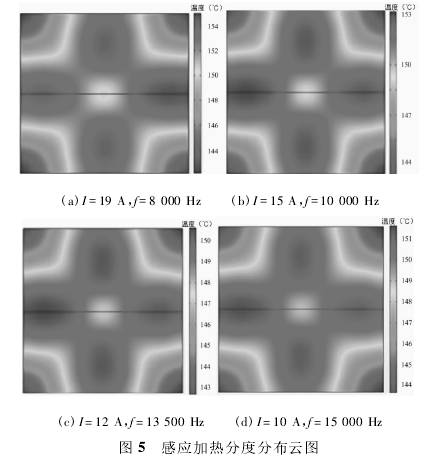
3输送带接头硫化加热系统的温度监测
3.1K型热电偶与多路温度记录仪
如图6所示,多路温度记录仪主要由触控液晶屏、按键、ARM微处理器为核心的主板、主电源、智能通道板、大容量FLASH等构成。记录仪的采样周期为1s,能实时显示数据图、柱状图、曲线图等。可以根据所布置的K型热电偶的数量,设置通道数目,对于每--路的温度补偿,支持补偿信号的输入,能够提供多种补偿模式”。含有与上位计算机通讯的标准.接口,将数据传输至计算机中,便于对后期数据的收集与整理。
K型热电偶主要包括感温元件、接线盒与保护套管等,将其与多路温度记录仪配套使用甲,可以保证温度数据采集的准确性,主要用于监测电磁感应加热方式下加热钢板的温度变化情况。
针对不同位置处的温度变化,结合仿真的4种电流下的温度分布云图,对多个K型热电偶进行排布,将其置于加热板的下表面,测温点的布置如图7所示。
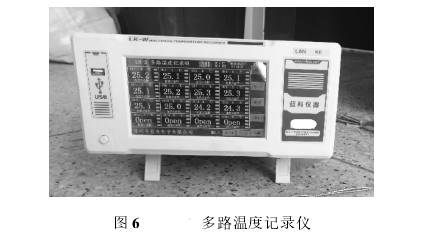
选取了12个测温点,分别对应温度监测系统的12个通道。研究沿钢板中心线方向(测温点1、2、3)、对角线方向(测温点4.5、7)、中心区域(测温点6、7、8、9)以及钢板下半部分(测温点9.10、11、12)的温度变化趋势,可以得到不同电流数值的工作状态下的温升曲线。
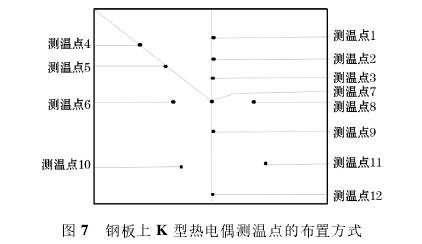
3.2温度数据的监测及分析
将传感器排布到钢板上,从平板硫化机的下加压板向上,依次布置下加热钢板、待硫化生胶、上加热钢板、上加压板,并按顺序对所需仪器进行接线,搭建好实验平台,输送带接头硫化感应加热的温度监测系统如图8所示。
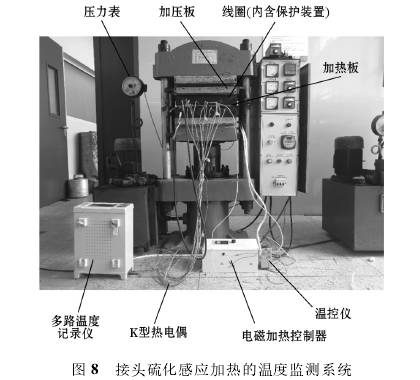
实验平台搭建完成后,扳动电源开关,电磁加热控制器开始工作。调节其控制面板.上的螺旋变位旋.钮,可以对电流、频率、电压等参数值进行设定。调整不同的电流(10、12.15、19A)后,多路温度记录仪会记录温度数据的变化(图9),得到沿中心线方向在不.同电流下的温度变化。
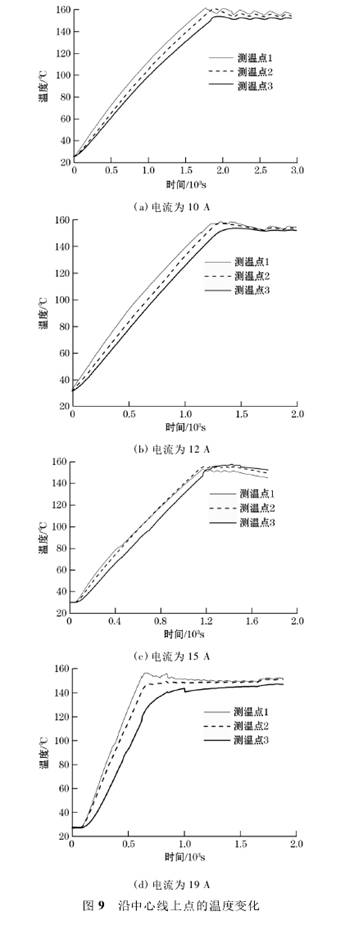
分析沿中心线位置的温度变化,电流为10A和12A时,1点位置温度最高,观察图5的仿真结果,1点处于整块钢板温度最高区域的核心部位,2点位于高温区域的边缘,3点处于加热死区的边缘,所以3点温度最低,随着电流的增大,电流由12A增大至15A,高温区域的热量分布会向钢板边角扩散,导致测温点1处的温度低于2处的温度,与加热死区接触部分的热量逐渐向外围扩散,导致测温点3处的温度较高,随着时间的推移最终高于2处的温度,由图9(d)看出,当电流为19A时,3个测温点在升温过程中的温差较大,强电流不易于保证升温的均衡性。
然后分析沿对角线方向(4、5、7点)在不同电流下的温度变化,得到如图10所示的曲线图。
由图10分析可知,当电流由10A向19A变化时,4点温度是最低的,原因是该点在钢板的边缘位置,受电磁感应影响较小,测温点7表示的是钢板的最中心位置,10A电流条件下,当热板温度稳定后,测温点5的温度高于7点,说明此时加热死区的面积较小,弱电流会使中心加热死区面积缩小,随着电流由12A向15A增大,中心加热死区的面积逐渐扩大,测温点5逐渐成为了加热死区的边缘部位,边缘部位热交换频繁,故此时其温度低于测温点7,当电流为19A时,如图10(d)所示,在强电流的作用下,由于加热死区外围温度升温较快,5点受其他区域热传导的影响,温度逐渐高于7点。
分析沿对角线区域的温度变化,随着电流的增大,在钢板加热过程中,不同点升温的快慢也不一--致,4点温升波动幅度较大,因为4点处于钢板边角部位,受感应电流影响较小,且与其他区域进行热交换不明显。电流增大的过程中钢板的升温时间逐渐缩短,且温度不均匀性也越明显。4种电流下(10、12、15、19A)下钢板升温至硫化温度所需的时间分别是29、25、.18、12min。
分析中心区域处(6.7.8.9点)在不同电流下的温度变化,得到如图11所示的曲线图。分析在热板中心区域,也就是加热死区部位的温度,以测温点6、7、8、9的温度变化来反映。由图11中可以得出,6、8 点位于加热死区边缘,随着电流的变化,加热死区面积也在改变,所以与周围区域进行的热交换较频繁,6点和8点能够较快速地吸收高温区域的温度,所以两者温度变化很频繁。
最后分析钢板下半部分(9、10、11、12点)在不同电流下的温度变化,得到如图12所示的曲线图。
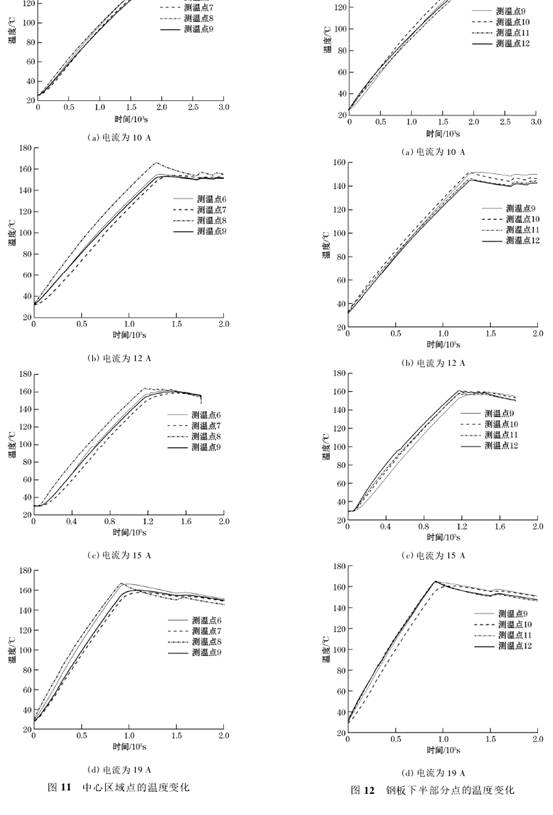
分析在热板下部分中间区域,以测温点9、10、11、12的温度变化来反映。由图12中可以看出,最终温度稳定后,测温点9、10的温度高于测温点11、12的温度。这是由于点11位于钢板下部边角与高温区域的接触处,此处是整块钢板温差最大处,测温点12位于接近钢板边缘处,此位置与空气之间会产生部分热交换,故此处温度偏低。而测温点9接近钢板中心,且其.周边温度热量较均衡,热损失较少,测温点10是钢板.热量最大处向周边蔓延的过渡点,所以两者温度较测温点11和12高。
结合图9~图12的数据,最终温度稳定后均能保持较小的温差,体现了加热效果的均匀性。
4结束语
针对现有输送带接头硫化加热方式存在的加热不均匀、接头质量差、加热时间长等问题,本文以电磁.加热控制器为基础,设计出了一种基于电磁感应的加.热系统,并通过仿真分析,建立了基于K型热电偶和多路温度记录仪的12通道监测系统,得到了钢板不同位置的温度变化规律和温升曲线,证明了此种加热方式能够使钢板快速达到硫化温度,且能使温度均衡分布,调节相应电磁参数可以最大限度降低温差,所设计的温度监测系统能准确地采集处理温度数据,这可以为后期构建高可靠性硫化系统的全息表达方式、形.成硫化系统智能监测平台提供了参考。