裂解炉热偶保护套管磨损穿透原因分析
发布时间:2021-03-11
浏览次数:
摘要:
裂解炉热电偶套管头部发生磨损穿透,单台炉子20个套管中有接近一半以上发生,其他套管头部也有不同程度的磨损,套管发生磨损的部位均在裂解气的来流方向,且套管头部端面有明显的腐蚀凹坑和沟槽。套管表面磨蚀穿透后COT测量值失真.严重影响裂解炉的正常操作。通过对热偶套管的结构改进,炉管COT偏差明显改善,各炉管的裂解深度保持一致,有效保证了裂解炉的长周期稳定运行。
乙烯是石油化工的基本原料,乙烯装置是石油化工生产的核心。当今世界90%以上的乙烯是通过管式炉烃类热裂解的方式生产的,裂解炉是乙烯装置最关键的核心设备,其控制效果的好坏直接影响乙烯的收率。裂解炉内反应复杂,各变量之间耦合度高。裂解原料在裂解炉炉管内进行的烃类裂解反应中,裂解炉的裂解深度是衡量裂解炉内裂解反应进行程度的重要指标,为了获得一定的乙烯收率,必须将裂解深度控制在适当的范围之内,目前国内大部分乙烯裂解炉装置均采用炉管出口温度COT(CoilOutletTempera-ture,以下均简写为COT)来表征裂解深度,为保证正常生产.必须对COT实现较为精确的控制。
1裂解炉COT平衡调节控制现状
1.1COT调节原理
中国石油兰州石化公司240万t/a乙烯裂解.装置HSII型裂解炉为2007年所建.每台炉生产能力为400万t/a乙烯,每台裂解炉共有40根1-1型炉管,它们在辐射室按南北方向分为4组排列,每组有10个1-1型辐射炉管,且每组的10个1-1型辐射炉管的出口上设有5个出口温度测量热偶,原设计热偶安装结构如图1所示。它们在辐射炉管的出口呈间隔排列,各组的5个炉出口温度的平均值做为本组炉出口温度调节器的测量值。通过这些出口温度值偏差的输出和调节,来达到平衡各组炉出口温度的目的,保证裂解炉各组出口温度满足工艺要求,从而控制好裂解炉的出口COT.
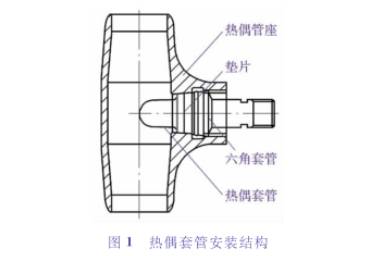
1.2裂解炉出口COT偏差现状
为了提高双烯收率和减少碳三生成量,对裂.解炉原料进行优化投乙烷,投乙烷过程中发现裂解炉COT温度偏高,原来设计投乙烷COT为837~853℃,而实际操作中投乙烷初期COT达到870~872℃,末期达到了875℃,这样的操作工艺条件会造成SLE有超温现象。而且,在裂解炉投油初期,裂解炉COT偏差小,但运行一段时间以后,COT偏差逐渐增大,最大时COT沿度超过30℃,个别炉管COT甚至达到900℃,并且发现相应安装热偶温度测量点的炉管结焦严重,甚至发生炉管堵塞。2011年大检修期间,发现裂解炉出口热偶套管头部有磨损穿透现象,磨损热偶套管如图2所示,单台炉子20个套管有接近一半以上磨穿,其它套管头部也有不同程度的磨损。套管发生磨损的部位均在裂解气的来流方向,且套管头部端面有明显的腐蚀凹坑和沟槽,后经堆焊修复,使用周期也不足半年。热偶保护套管发生磨损甚至磨穿后,热偶将直接外露于裂解气中,裂解气中的焦炭将附着于热偶表面,致使温度热偶传感器不稳定发生温度漂移,COT测量值发生失真,从而影响该组总的炉管出口温度,整台炉子的裂解深度将无法控制,严重制约了裂解炉正常生产运行。
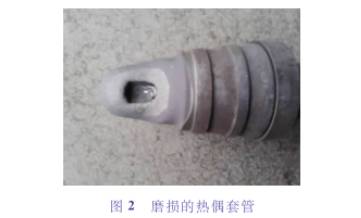
2热偶套管磨损原因分析
2.1冲蚀磨损
通过对热偶套管安装结构及套管发生磨穿的位置进行研究,发现热偶套管原设计存在不足,所有COT套管头部伸进炉管流道约30mm,即套管头部接近炉管中心,因套管头部伸进炉管流道内过深,减少了裂解气流通面积,据估算约占炉管30%的流通面积,大大增加了裂解气的流动阻力。高温下裂解原料在炉管中发生复杂的热裂解反应,反应除生成乙烯、丙烯、丁二烯等期望产品外,还伴随有炔烃、芳烃、焦炭及硫化物、氢气和二氧化碳等物质生成。裂解炉出口裂解气组成非常复杂,为气、液、固三相混合物,其中还含有H2、CO、CO2、H2S等腐蚀性气体”。裂解气流经套管头部端面时,因套管伸进炉管流道约30mm,改变了炉管内裂解气的涡流特征,裂解气遇到凸起部位突然改变流动方向,温度下降.阻力增加。正常生产中,流经炉管的裂解气流速约达到100~140m/s,裂解气中温度高达860℃的汽液混合物以及其中夹带的焦粒对伸出的套管头部产生冲刷,其中的焦粒由于质量较大,更具有较大的冲击力,对套管产生严重的冲刷破坏,热偶保护套管在炉管内既承受裂解气中焦炭颗粒的冲刷,造成冲蚀磨损,又承受高温酸性气体的腐蚀作用,在两者的综合作用下,热偶套管伸入炉管的头部成为磨损最为严重的部位,进而发生磨蚀穿透。这是套管发生磨蚀穿透的主要原因。
2.2金属尘化腐蚀
另外,热偶套管的材质为Incoloy800H,是一种广泛应用于高温结构件的奥氏体耐热合金。在H。-CO-CO2-H2O环境和温度为800~950℃条件下,套管材料Incoloy800H的组织易发生渗碳,这将会导致合金套管严重脆化,甚至腐蚀造成套管壁厚减薄,即所谓的金属尘化腐蚀与。研究表明,金属尘化通常发生在温度为550~900℃,其主要表现为金属快速损耗、变薄,最终导致金属碳化和粉化。金属尘化的机理是金属在严重渗碳后的体积膨胀量相当大,表面的不均匀渗碳将会在金属局部区域内产生很大的压应力,当该区域内应力达到--定程度时,就可能碎裂、剥落,发生所谓的金属尘化。金属尘化是一种物理作用的高温腐蚀,是一些金属(如铁、镍、钴及其合金)在高温碳(碳氢、碳氧气体)环境下碎化为由金属碳化物、氧化物、金属和碳等组成的混合物而致金属损失的行为3。流经炉管的裂解气中含有一一定量的H2.CO.CO2和H2O,温度在840~860℃,这就为套管的渗碳提供了条件.这也是导致合金Incoloy800H套管管壁出现腐蚀凹坑和沟槽的主要原因之一。
3改进措施
3.1热偶套管结构改进
要想炉管的COT测量值准确稳定并且延长套管使用寿命,就需对套管结构进行重新设计。结合热偶套管安装结构尺寸及套管端部发生磨损部位,分析认为套管头部伸入炉管太深,流经套管头部高温裂解气的冲刷腐蚀是套管磨损的主要原因,因此需将伸入的套管头部适当缩短,以减少裂解气的冲刷腐蚀作用。热偶套管的结构如图3所示。为了减少热偶插入深度对所测COT的影响,经过分析研究,决定将套管头部由40mm缩短20mm,同时,为使套管与原来的热偶长短相配合,将热偶头部缩短的20mm延伸至套管尾部套筒,这样改进后的热偶套管头部既从炉管中心外缩至炉管内壁附近,又满足与原来的热偶完全配合,从而避免了缩短热偶对裂解炉COT的影响。热偶套管缩短改进后的安装结构如图4所示。
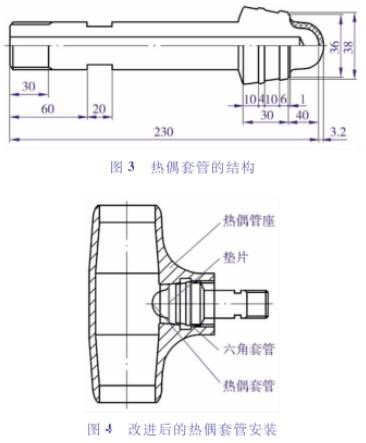
3.2热偶套管表面涂层
在套管结构改进的基础上,为了防止套管与高温裂解气直接接触发生渗碳和金属尘化,还对套管头部进行了表面涂层保护处理。采用钴铬钨涂层分两层喷涂,每层厚度不小于1.6mm,硬度HRC大于37,涂层进行渗透检查,同时外表面进行打磨处理,表面粗糙度为1.6。涂层的化学成份如表1所列。
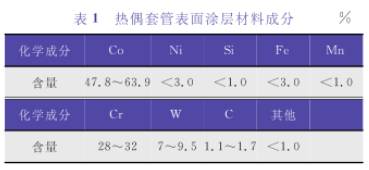
4结语
分析裂解炉热偶套管的磨蚀穿透形貌,找出.了套管磨损穿透的原因,裂解炉热偶保护套管经改进投用后,炉管COT偏差较之前有明显改善,各炉管出口COT偏差≤5C,这为裂解炉的优化操作提供了准确的依据。通过准确的测量炉管出口裂解气的真实温度,可以有效控制各炉COT偏差,使各炉管的裂解深度保持一致,从而为炉子的整体优化操作提供了条件,有效地改善了炉子的运行环境,保证了裂解炉的长周期稳定运行。